Phone: (248) 773-8055
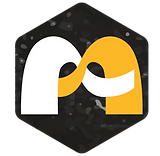
PROJECTS
Our most important goal is to team with our clients and better understand their core necessities and goals. This creates a shared vision of what quality processes and extraordinary results look like. Below are some examples of the work we’ve done - take a look, and get in touch to learn more.

John F. Kennedy International Airport, Detailing Support Steel
At JFK International Airport, we undertook a pivotal role in enhancing infrastructure by using Tekla Structures to detail support steel for the new concourse and arrival terminals. Our expertise extended to crafting robust catwalks and support steel systems vital for seamless baggage handling operations.
GM Factory ZERO, Hamtramck
Magnum Consulting engineers played a role within General Motors' first fully dedicated electric vehicle assembly plant called Factory Zero. Our team designed six trim lines of tool rail steel, including the modular support steel, access catwalks, and standard components. We also developed and designed a modular support structure that was pre-assembled and tested before installing in the plant, allowing for an efficient installation and reducing worker risks. We also developed standard components for utilities (brackets, stands, etc.) and designed operator platforms for multiple trim lines.
Volvo New River Valley Truck Plant - Vertical Drop Lifter
Magnum designed VDLs for Body Shop Pallets in Virginia's Volvo Truck Plant at the beginning of a Body Shop Framing line. The design is for a 1500 kg live load, which includes a machined base on the lower level. The VDL places an empty pallet on the precision base, and a robot loads a floor pan onto the pallet. At the end of the framing line, the completed truck cab transfers to a separate skid, a 2nd VDL lifts the empty pallet to an overhead mezzanine, and Magnum-designed roll beds return the empty pallet to the beginning of the line. Magnum is also designing the Pallet to Skid Fork Transfer with an Auxiliary Lift.
Stellantis Screen Guard and Structural Support, Mack Ave and Warren Truck Paint Shop
Magnum provided design, detailing, and Professional Engineering certification for the screen guard and platforms that support skid conveyors in the new Stellantis Mack Avenue Paint Shop. Magnum also provided design, detailing, and Professional Engineering Certifications for the PTED conveyor drives and take-ups at the new Mack Ave Paint Shop and the new Warren Truck Paint Shop. The drives were a new design for an Air-bi-dip Conveyor.
CAMI Production Platform
Magnum’s design team engineered the operator platforms around our customer’s robotic glass cell. The platforms included stairs, handrails, and special access points to equipment and material stored alongside and under the platform frames. Special care was taken to integrate these platforms with the surrounding tooling and provide ample access to all areas. The engineering also included providing stair access and handrails for egress.
HTI Cybernetics – GM, Oshawa Tailgate Lift Assist
Provided design and detail of a complex tailgate lift assist for a General Motors truck plant. This tool is used for rotating and installing the standard tailgate as well as transferring the multi-function tailgate between the truck and a separate carrier. Magnum had to integrate the layout and tool design with both changes in the plant assembly line and personnel space and clearance requirements.
Vin Etch Robot Towers - GM, Spring Hill
Magnum engineered two support towers for robots responsible for etching the VIN number in a new vehicle. Engineering included footing design, modular column design, and surrounding platforms. One unique feature of the towers is that is it made of multiple small sections of API Tube that allow for the towers to be dismantled in sections. This design allows our customer to remove the robot with a fork truck even though it usually rests on the top of the 13’ tall assembly.
Treva Automation: Kuka - GM, Wentzville
Lead controls hardware design. Our team also provided electrical designs in ePlanP8 for new cells and tooling. We added new robots and tooling stations to accommodate new vehicle models. Created kits for existing robots and tooling stations to provide detailed instruction and bill of materials for replacement and addition of controls devices. Provided all necessary power calculations and checklists as required by the customer.
Automatic Systems Inc. - GM, Spring Hill
Magnum provided engineering studies, designs, and fabrication details for carriers, auxiliary lifts, and fork transfers. These designs supported the addition of new vehicles within the plant. The project required coordination with General Motors corporate, General Motors Plant personnel, and various contractors.
Versa Handling - FCA, SHAP, Tooling White Steel
Provided design and detail of support steel systems that hung all the new line-side tooling and utilities to build the latest model. Engineering included sizing of support steel members, field checking existing interferences, and coordinating with the fabrication shop. Engineering also included the design of a floor support structure for the BSR booth allowing workers to drive a full-size pickup over the structure into the work station
DMW - GM, Lordstown, Tire & Wheel System
Replaced outdated tire and wheel delivery conveyors to a new CDLR conveyor. Provided layout and design of new CDLR sections, and coordinated between customer, installer, and third-party equipment supplier. Also designed and detailed falling parts guard, conveyor support steel, access ladders, and walkways.
Central Conveyor - FCA, Belvidere, Paint Shop Upgrades
Updated/Upgraded conveyors in paint shop to support the launch of a much heavier and larger vehicle in the Belvidere Assembly Plant. The project involved splitting conveyors, re-routing conveyors, adding new chains, drives, and take-ups, widening falling parts guard, and upgrading support steel.
General Motors - Arlington, Chassis Extension Project
Provided project oversight for the development and installation of inverted power and free chassis conveyors. Magnum assisted with project planning, schedule reviews, and on-site construction support. Magnum also provided daily progress reports and safety reviews to prospective customers.
General Motors - Lake Orion Carriers
Provided design and detail of carrier and carrier transfer. Changes required to run the new product through all body, paint, and general assembly systems. Engineering included a rework of chassis clamshell carrier, PTT overhead carrier, etc. Reworks also included new product touching details for the end of arm tool (EOAT) on the paint shops underbody sealer robots.
Durr, Harley-Davidson - York, PA
Magnum provided path layout, support steel layouts, and screen guarding layouts of the new "frame line" conveyor system extension. Magnum also provided detailed fabrication drawings of track components; new drive addition, floor support steel, and building header steel as well as chain pull calculations for the entire system.
Genesys Systems Integrator - Ford Cuatitlan, General Assembly Rework
Provided engineering services for the rework of several automation systems required to start the production of a new product. Engineered two overhead power and free vertical drop lifters that can pull a product off an AGV or set the product on a flat-top. Other tasks included a rework of the skid system, chassis overhead power and free system, flat-top shuttle, and skillet fork transfer.
JP Cullen - DCX, Belvidere
Magnum provided steel design and details to an existing 6” OHP&F system to bring the hanging centers within corporate guidelines. 90 bays of conveyor were field checked to determine where extra steel was required. Field measurements taken while on-site by working in the trailer to ensure the accuracy of the new details. The material was then ordered, fabricated, and installed in a satisfactory and efficient manner.
DMW - FCA, Windsor
Developed design layouts and details for the new Headliner Decouple project at the Daimler-Chrysler Windsor Assembly Plant. Responsibilities included: path layouts, cross-sections, conveyor component details, header steel layouts and details, kip load calculations, conveyor chain pull calculations, and field checking.